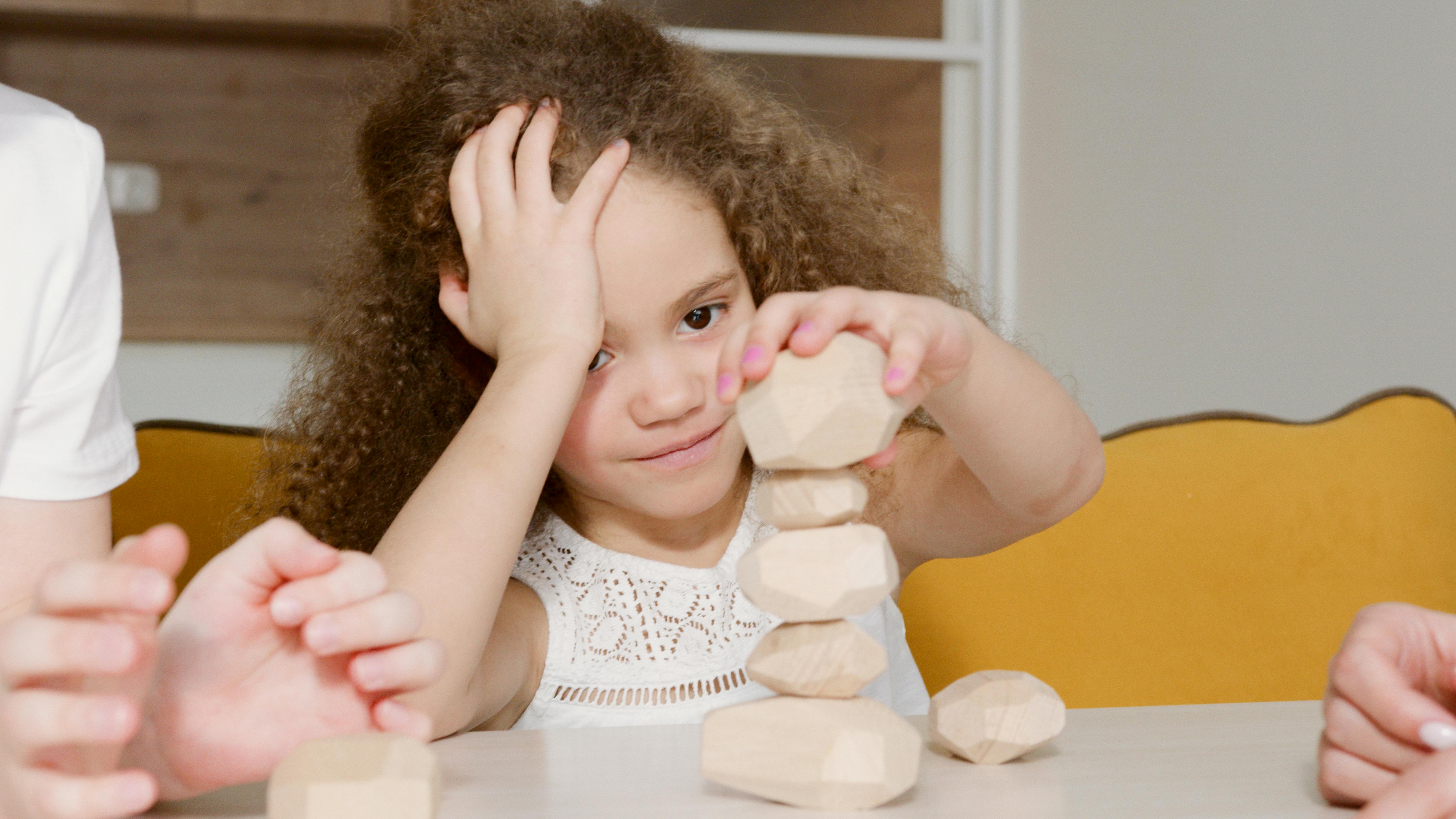
Selection criteria for belt drives and standards of use
To fully specify a belt, the material, length, and cross-sectional size and shape are required. In addition, timing belts require the size of the teeth to be provided. The length of the is the sum of the central length of the system on both sides, half the circumference of both pulleys, and the square of the sum (if crossed) or difference (if open) of the radii. So when dividing by the center distance, it can be visualized as the center distance multiplied by the height which gives the same squared value of the difference in radius on, of course, both sides.
Fatigue is the reason for most belt problems. This wear is caused by the stress of rolling around the pulleys. High belt tension, excessive slippage, harsh environmental conditions, and overloads caused by shock, vibration, or shock to the belt all contribute to fatigue. In the clockwise rotation of the driver, the driver pulls the belt from the lower side and passes it to the upper side. Therefore, the tension in the lower side belt will be greater than that in the upper side belt. Therefore, the lower side is called the tight side and the upper side is called the loose side.
Power transmission in belt drive is caused by friction between the belt and the pulleys. However, there will always be some relative movement at the driver belt interface and the belt driven pulley interface due to ineffective friction. This phenomenon is called belt slippage. Due to slip, its speed will be less than the peripheral speed of the sprocket and slightly greater than the peripheral speed of the sprocket.
There are many criteria for the selection of belt drives. They are built under the following required conditions: speeds and power transmitted between drive and driven unit, adequate distance between axes and appropriate operating conditions.
The open belt drive has parallel shafts that rotate in the same direction, while the cross belt drive also has parallel shafts but rotate in the opposite direction. The former is much more common, and the latter is not appropriate for standard and timing V-belts, because the pulleys contact the inner and outer surfaces of the belt. Non-parallel shafts can be connected if the center line of the belt is aligned with the center plane of the pulley. Industrial belts are usually reinforced rubber, but sometimes leather types, non-leather non-reinforced belts, can only be used in light duty applications.